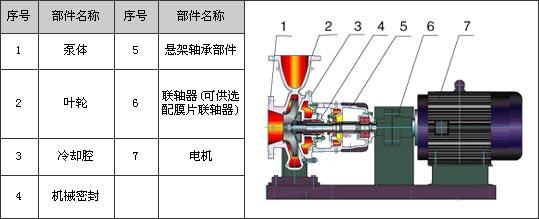
概述
AY/TY-RR型离心油泵系列,是在Y 型 离心油泵的基础上,消化引进国外先进技术进行设计的。它是为更好地满足用户的需要,以提高可靠性和节能为中心的设备更新换代而发展的新产品。该产品系列可用在石油精制、石油化工和化学工业,输送不含固体颗粒的石油,液化石油气和其它易燃易爆或有毒的高温高压液体。其特点有:
1、轴承体部件全部采用先进的滑动轴承和轴向推力轴承。
2、水力过流部件采用了高效节能泵的水力模型,效率平均比Y型油泵高2~5%。
3、为保持继承性,AY型油泵的结构形式、安装尺寸、性能参数基本保持与Y型油泵相同。
4、零、部件通化程度高。
5、根据使用条件的不同,主体部件选用Ⅱ、Ⅲ类材质,轴承体等零部件增加铸钢,铸铁两种。为寒冷地区、露天使用、船用等提供了选材方便。
6、轴承的冷却全部采用水冷。
AY/TY-RR型 离心油泵性能范围:
流量:Q=6.25~155m3/h,扬程H=70~603m,被输送介质温度T=-20℃~+300℃
泵结构
AY/TY-RR型 离心油泵为径向剖分节段式结构,穿杠将吸入段、中段、吐出段连成一体。泵转子由装在轴上的叶轮、平衡盘(鼓)等零件组成。轴向力由平衡盘,平衡鼓和推力轴承平衡。
轴承:采用径向滑动轴承,推力轴承采用向心推力轴承,平衡残余轴向力。
轴封:采用填料密封或机械密封,根据用户需要而定。
传动:泵通过联轴器由原动机直接驱动,从原动机看泵为逆时针旋转。
管路系统:冷却水是根据介质温度和使用要求,对轴封腔、轴承或泵支架等进行冷却。
水量每支管路建议为0.2~0.5m3/h,压力为0.2~0.3MPa。密封冲洗是根据泵输送介质、温度及压力等工作条件不同而不同的。每个泵腔的封液量如下表(内供或外供均可)。
密封名义直径
(mm)
|
13-47
|
48-59
|
60-84
|
85-95
|
96-133
|
平均封液量
(m3/h)
|
0.18
|
0.24
|
0.36
|
0.48
|
0.66
|
密封液的压力一般要高于密封腔的压力0.07~0.1Mpa。若输送介质属于易汽化的,则应高于汽化压力0.175~0.2Mpa。蒸汽管路是当输送介质的温度降低而析出晶体时配备的,其压力为0.1Mpa左右。
四、泵用材料
材料类别
|
Ⅱ
|
Ⅲ
|
使用温度(T)
|
-45℃~+300℃
|
-45℃~+300℃
|
零
件
名
称
|
壳体(体、盖)
|
ZG230~450
|
ZG1Cr13Ni
|
叶轮
|
ZG230~450
|
ZG1Cr13Ni
|
轴
|
35CrMo
|
35CrMo
|
壳体密封环
|
ZG1Cr13MoS
|
ZG1Cr13MoS
|
平衡盘(鼓)
|
ZG1Cr13NiMo
|
ZG1Cr13NiMo
|
导叶
|
ZG230~450
|
ZG1Cr13Ni
|
五、泵的装配
1、泵装配质量的好坏对泵的性能及运行影响显著。
叶轮出口中心与导叶进口中心的对准,泵的转子部分与定子部分的各个密封间隙值大小均匀等稍有偏差,就会使泵的性能受到影响,流量减小,扬程降低,效率差,以致降低泵的使用寿命,为此,本泵必须有良好的同心度方能使泵运转轻快,故在装配时务必注意。
2、转子部件技术要求:
泵体密封与叶轮密封环的名义径向最小运转间隙,按下表:
名义尺寸(mm)
|
<50
|
50~99.99
|
100~199.99
|
200~324.99
|
325~449.99
|
450~574.99
|
575~649.99
|
最小直径(mm)
|
0.25
|
0.28~0.35
|
0.38~0.48
|
0.50~0.60
|
0.63~0.73
|
0.75~0.85
|
0.88~0.95
|
注:对于大于649.99mm的直径,最小直径间隙应当是0.95mm加上每增加1mm直径加1μm或增加相应的百分比;对于咬合趋势较大的材料和(或)工作温度大于260℃的各种材料,应当在上述直径间隙再加上1251μm.
3、泵的装配顺序,可参阅《14·泵的拆卸》按拆卸顺序反向进行。装配完毕后,用手转动转子,检查泵内是否有摩擦声或转动不灵活等不正常现象。
六、泵的安装
1、安装时需要的设备
泵安装需要下列常规的和专用设备和工具:
a、 负载能力合适而安全的起吊设备;
b、每个地脚螺栓处都必须备有一块钢的垫铁或楔铁,作找平底座用;
c、 灌桨的材料必须是不收缩的灌桨料。为了灌桨准备一个木盒,而且需配有漏斗。
2、泵的搬运
在搬运泵时要注意安全以防事故发生,搬运时注意下列事项;
a、 在搬运时,起重机的吊钩应挂在底座上的用于起吊耳或吊孔(一般为4个)上,不允许吊在泵和原动机的螺栓孔或吊在泵的轴承体上,更不能在泵轴处起吊;
b、起重负载应均匀平衡,且注意起重设备的承载能力,起吊时应小心谨慎,防止泵件的碰撞。
c、 严禁异物或灰尘搬运过程中进入泵和电动机内。
3、泵的开箱检查
泵运到使用单位后应开箱检查泵的零件是否丢失,是否在运输过程中有损坏,如果了出现有丢失或损失时,应立即向运输部门和泵制造厂声明。
4、贮存
如果泵需要在安装以前库存一段时间,泵仍然包装,而且应放在干燥、防雨、防灰尘的合适的地面上,泵的吐出口和吸入口应盖住发防异物进入。
泵的轴和其它精加工的零件应注意防潮,应涂保护油层。
5、泵的基础
① 泵的基础必须是具有足够强度和尺寸的混凝土地基。混凝土水泥可以选取用400号普通水泥,黄沙必须是不含泥土和其它杂质的纯净粗沙,石子为坚实的卵石和碎石,水泥的混合比例为1:2:5,即1份水泥,2份沙子,5份石子,在灌水泥时,在选靠近地面和高出地面的部分应放有木模框,二次灌桨原材料标号应比基础材料高一倍,机组安装就位后的现场浇灌,施工时必须浇捣密实均匀与原混凝土结合良好。基础的质量约等于机组质量和3~5倍,泵的地基应比泵的底座长出50~70mm,且要留出地脚螺栓孔(孔φ100)。
② 地基包括如下内容:地基的地脚螺栓孔的定位,灌桨和留出外联管路位置,然后在其余空间灌桨。
③ 地基的表面可以是粗糙的,以使灌桨效果好。
④ 地基完全固化后再安装设备。
6、搬放和找水平
① 在底座下面放置钢的垫铁和楔块调整垫,一般都放在地脚螺栓处,如果底座较长,在两地脚螺栓的中间右放置一块垫铁。
② 检查底座下的地式,清洗灰尘,油和其它杂物。
③ 起重吊钩吊住底座原吊耳或吊孔,把底座吊在地基上方,慢慢地安放底座,并对准每个地脚螺栓孔位置。
④ 用一个刀口平尺和机械水平仪放至安装泵和电机底脚加工平面上,用调整楔块或 调整垫的厚度来确定底座在各个方位上的水平,推荐每100mm长度不平度小于0.25mm,这时地脚螺母拧到适当的程度(不能过紧),楔块或调整垫应紧固。
⑤ 底座找平。而且和地脚配合较紧后再灌桨。
7、底座的灌桨
① 混凝土基础至少固化7天后,才能灌桨。
② 为了保证除去灌桨部位低强度的、疏松的混凝土,在灌桨之闪,应用一把尖锤把水泥基础材料的顶部刨掉约10~25mm;
③ 所有的润滑脂、润滑油、油漆、水泥布的沫状物和其它杂物都应多需要灌桨的表面除去。粗糙的混凝土表面应当用油压缩空气吹去灰尘和松散和颗粒。如果有采用水泥砂桨,混凝土表面应当用水浸透,直到不再吸水为止,多余的水应该除去。
④ 底座应该放置在要求的位置上,把底座支承在楔形调整垫上调水平的螺钉上,并用地脚螺栓把底座固定在边沿的底部的刨凿过的基础顶部之间允许有大约25~50mm灌桨空隙。
⑤ 在灌桨之前,地脚螺栓预留孔中的所积水和外来杂物都应除去。
⑥ 如果在灌桨之后还存在空洞,可以使用环氧砂桨来充填这些空洞,如果灌桨用的是水泥泥桨,则在应用环氧砂桨补空洞之前,建议让水泥砂桨先经过整28天的固化。在已发现的空洞处通常用手压泵来灌补环氧砂桨应当极其小心以保证不使压力过大以免把底座顶翘曲,每个空洞至少应该钻一个通气小孔以防压力过大。
⑦ 灌桨后,进行泵和电动机的调正工作。
8、设备的调整
设备至少应在下面三个时期检查设备。进行调正;
第一次,泵的底座已拧紧,但电机没拧紧;
第二次,泵和电动机已紧固,但吸入和吐出管路法兰的螺栓没紧固。
第三次,在运转24小时后,再检查一次,检查后把泵降原动机紧固。
在调正过程中应注意以下事宜:
a、在调正以前,检查全部管路,保证它们不对泵底座产生作用力或力矩;
b、在调整泵和电动机轴中心线时对正时,垫片应垫在电动机下面;
c、泵和电动机在联轴器连接好以后,重新检查其对中性;检查电动机的转向是否符合泵轴的转向,从联轴器方向上看泵,为逆向旋转,如果电动机转向不符合泵的转向,必须把电动机转向调整过来。
9、安装注意事项
① 泵吸入管的高度、长度和管径应满足设计要求,并保证工作时不超过其允许汽蚀余量;
② 吸入和排出管应有管架,不允许承受管路的外加负荷;
③ 吸入管路应短而直,管的直径要大于泵吸入直径1-2倍,同时应用偏心收缩径管连接,泵吸入管路应做成尽量大的弯曲半径;
④ 校正泵和原动机轴的同心度。,在联轴器外圆上偏差允许≤0.10mm,其端面偏差≤0.05mm;
⑤ 在管路安装及确定原动机转向方向后,再装上联轴器。
七、运转
1、开车前的准备
① 对轴承体加油,推荐轴承润滑油是22号或30号汽轮机油;
② 接通冷却水,密封如果是外冲洗,则供上封油;
③ 打开吸入阀和排出阀,把泵内灌满液体,然后关闭排出阀;
④ 接通电源,点车[开车立即停车],观察泵轴旋转方向是否是逆时针方向;
⑤ 输送热油时,在开车前要均匀预热,预热是利用被输送的热油不断能过泵进行的,预热速度率推荐40℃~50℃/h
2、运转
① 打开泵的吸入阀;
② 关闭吐出管路的阀,使泵内充满液体;
③ 启动电机,接着逐渐打开吐出管路的阀
④ 起动油泵打开压力表,逐渐打开出口闸阀到压力表指针指到规定所需的位置为止,当泵的压力上不来时,立即停车检查;
⑤ 起动后,立即打开泵的排出阀,决不允许泵的排出阀关闭较长时间,以防过热引起泵的损坏;
⑥ 运转后,一般观察泵的压力、电流等,是否在正常使用范围内。不宜在低于最小连续稳定流量下连续运转,如果泵没有给出最小连续稳定流量,则不应低于30%设计流量下连续运转。
⑦ 不能用吸入管路上的闸阀来调节流量,避免产生汽蚀;
⑧ 正常运转时检查振动,在轴承体上测量的滤波振动不超过峰值速度7.6mm/s;
⑨ 当泵已经达到运转的温度和压力后,再次检查调整,如果需要的话应重调(微调)设备;
⑩ 运转24h左右,在泵体水平支承面上打锥销,如原动机地脚允许的话,也要打锥销,其直径大小视空档位置而定。
八、停泵
1. 关闭吸入压力计和吐出压力计;
2. 慢慢关闭泵的吐出阀;
3. 关闭电动机;
4. 当泵停稳后,再关闭泵的吸入阀。
九、维护
1、定期检查轴承发热情况,轴承温度不应超过80℃;
2、轴承和轴承室应有良好润滑;向轴承供油的甩油盘或油环的工作淹没油位,应当高出甩油盘的底部或油环孔的底部3~6mm;
3、每隔8小时换班时都要对油杯进行检查,检查油杯油位是否正常;
4、建议每隔半年把油排掉、冲洗,然后再加新油。一般情况下,在春秋两季进行,对于潮湿、沙漠地区、气候变化大的露天现场,还必须勤换油;
5、泵的滑动轴承;轴承室内必须加清洁的润滑油,要勤加油,勤换油,否则会烧瓦。当修复或更换轴承时,轴瓦需刮研,轴瓦与轴的配合面接触点应达到85%;
6、对装置上的备用泵,要定期旋转转子部件,建议一个星期旋转一次,每次90°左右,以防变形,同时保持轴承润滑油膜;
7、对于装置的高温备用泵,还要保持一定温度,以备待用。
十、泵的拆卸
1、拆卸泵时应注意下列事项:
a、 先按停泵程序停泵;
b、将泵壳内液体放掉(如有冷却水管时也应放掉水);
c、 将轴承室内的润滑油放掉;
d、 拆去妨碍拆卸的附属管路;
e、 拆卸联轴器;
f、 拆卸泵罩
2、拆卸顺序:
泵的拆卸步骤从拆下吐出侧的轴承部件开始,其顺序大体如下:
a、 拧下吐出侧轴承室盖上的螺栓和轴承体与托架、托架与尾盖、上轴承体与下轴承体之间的联接螺栓,以及轴上的圆螺母。卸下止推滑动轴承部件及托架。
b、拧下机封压盖上螺栓和轴上的轴套螺母,卸下机封压盖、轴套及机械密封。
c、 拧下尾盖、吐出段之间的螺栓,依次卸下尾盖、隔板以及轴上的卡环和平衡盘。
d、 拧下穿杠螺母,卸下吐出段;卸下吐出段中的平衡鼓,末级导叶。
e、 卸下末级叶轮和键后,卸下吐出段(包括导叶在内)按同样方法,继续卸下其余各级的叶轮、中段和导叶,直到卸下首级叶轮为止。
f、 拧下吸入段、托架、轴承体之间的联接螺栓,拧下上轴承体与下轴承体之间的联接螺栓,卸下滑动轴承部件和托架。(在这之前应预先将联轴器部件卸下)
g、拧下机封压盖上的螺栓及轴上的轴套螺母,拆下机封压盖、隔板、轴套及机械密封。
h、最后将轴从吸入段中抽出。
至此,拆卸工作基本完成,但在上述过程中,还有部份零件互相连接在一起的,一般情况下,拧下联接螺栓或螺母即可卸下。
泵的装配顺序,一般是按拆卸顺序反向进行。
3、清洗和检查:
a、 清洗全部的零件,在空气中干燥或用布擦干。
b、检查全部零件的磨损情况,对不能确保正常运转的零件应更换新的。
c、 检查泵轴是否有灰尘或生锈,用千分表检查轴的不直度。
d、 当密封环间隙超过推荐值的最大值50%时,应更换密封环零件。
150AY150,150AY150X2
长沙天鹅天欧工业泵品牌服务承诺:
产品在质量保证期内,对有缺陷的产品负责包修、包换、包退;所有质量问题投诉,24小时内作出答复。外派服务人员,做到故障不排除或未作出结论意见,不撤离现场。我厂所出厂的配件均为原装尺寸配件。我厂现生产的产品及配件与原有型号通用、通配,如出现安装尺寸及质量问题我们将无条件退换货,所有设备服务终身!(整机保修一年,易损件保修六个月)。
全国各区域售后部联系方式:
售后总部
湖南长沙 400-1801-181
(其他各区域售后联系方式,敬请来电索取)